In the beauty industry, high-quality packaging solutions have always attracted much attention. As a high-quality packaging material, the sealing performance of acrylic cream jar has attracted much attention.
As a packaging material mainly made of acrylic resin, acrylic cream jar has excellent chemical resistance and heat resistance. This not only effectively prevents the product from external contamination and oxidation, but also prolongs the shelf life of the product. In addition, acrylic resin also has low permeability, which can effectively prevent moisture and air from entering the container to ensure the freshness of the product.
In addition to the choice of materials, the sealing performance of acrylic cream jar is also closely related to the closure method. Common closure methods include rotating caps, press caps and magnetic adsorption caps. Regardless of the closure method, the key is to ensure a tight fit between the container and the lid. Therefore, the accuracy and quality of the thread structure are key factors in sealing performance. At the same time, the magnetic adsorption cap also needs to ensure the strength and stability of the magnetic force to ensure a tight closure.
In addition, the sealing gasket is also an important factor affecting the sealing performance of acrylic cream jar. The sealing gasket is usually located between the container and the lid to play a filling and sealing role. Choose the right sealing gasket material with good elasticity and chemical resistance, which can effectively prevent air, moisture and other contaminants from entering the container. At the same time, the quality of the sealing gasket also needs to be guaranteed, such as uniform thickness and smooth surface, to ensure a good sealing effect.
In addition to the choice of materials and closure methods, the production process is also an important factor affecting the sealing performance of acrylic cream jar. During the production process, it is necessary to ensure the dimensional accuracy and consistency of the container and lid. If the dimensions of the container and lid do not match, it will lead to a loose seal and affect the sealing performance. At the same time, the surface treatment of the container and lid, such as deburring and polishing, should also be paid attention to during the production process to ensure a smooth contact between the container and lid, so as to achieve a better sealing effect.
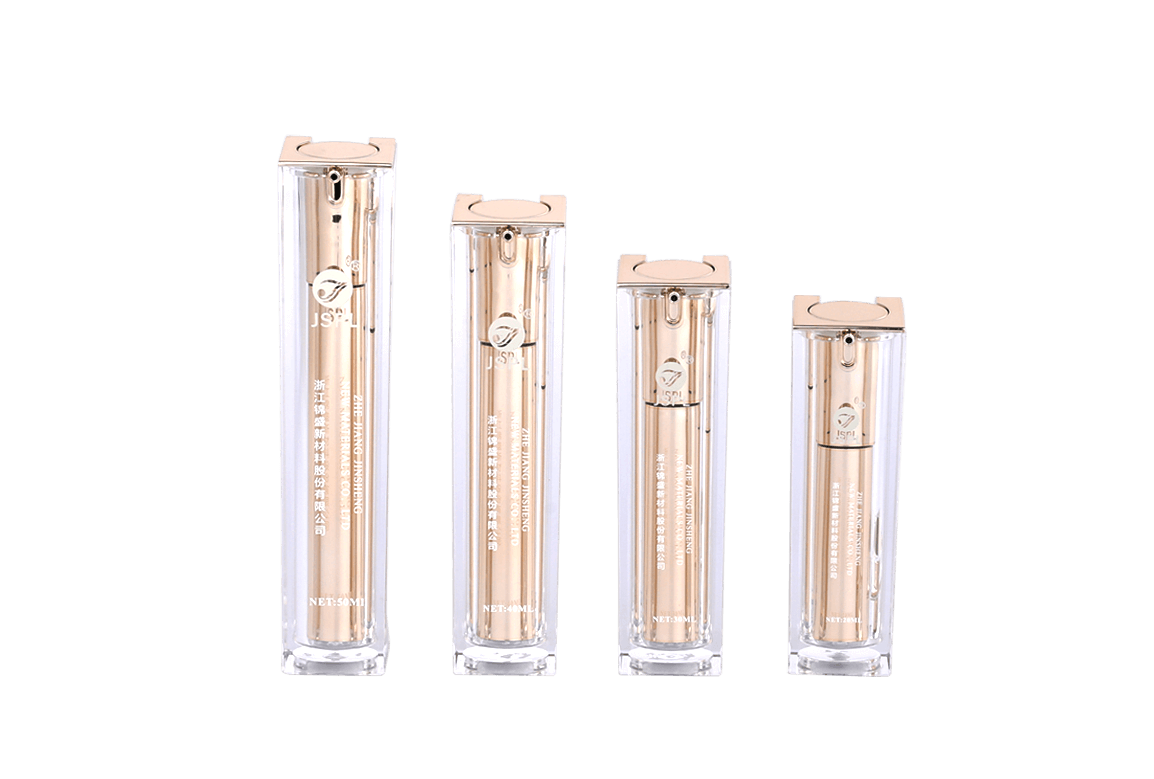